In this article we’ll talk about the right way to replace brakes, from selecting parts, to machining rotors, to cleaning inspection, and lubrication. Brake replacement is NOT just putting new pads on, or at least it shouldn’t be if you want brakes that work well. People from our potential customers, to DIYers, to people who want to learn to shop for brake service may benefit from this information.
Useful information, even if you’re not in Berkeley
Our shop is in Berkeley, and we’d love for you to come to us for brake repair if you’re nearby, but for most of the world that won’t be possible.
But even if you can’t come to us, you can learn what makes a good brake job and ask questions before you choose a mechanic.
While there are some bad actors in our field, there are also a lot of really great people working at great auto repair shops. Hopefully this will help people find a thorough, competent, and caring mechanic.
brake replacement – The “how” matters
When people think about automotive brake repair, replacing brake pads is usually the first thing that comes to mind, but there’s a lot more to auto brake repair than just pads.
Don’t get me wrong. Using good pads is probably the most important aspect of a brake system, but without skill and care, a brake job may not turn out so well.
Short service life, pedal pulsation, brake noise, uneven braking, and uneven pad wear are all common problems that are usually avoidable.
Every repair needs to have several items addressed:
- cleaning
- inspection
- lubrication
- restoring brake disc condition
- replacing all missing and worn parts
Replace with the best brake pads
If you don’t want car brakes that fade, have poor bite when cold, wear out quickly, or make annoying noise, buy genuine pads from a dealership.
Do they cost more? Typically, they do. Are they “better”? Typically, they are.
When deciding what make pads “good”, you have to consider what’s important to you. For instance, if I wanted the best brake pad for racing, buying a Genuine Subaru pad set might not be the best choice.
However, when a brake pad is very good at one thing, like fade resistance, it loses other positive attributes, like the ability to stop well when cold. If you want a pad that does everything fairly well, buying them from a dealership is the best bet.
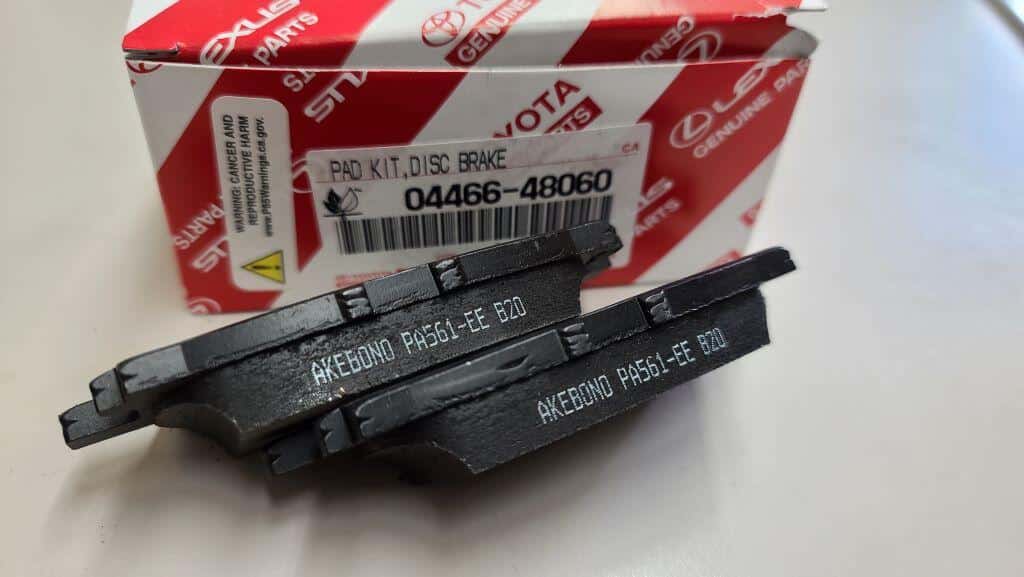
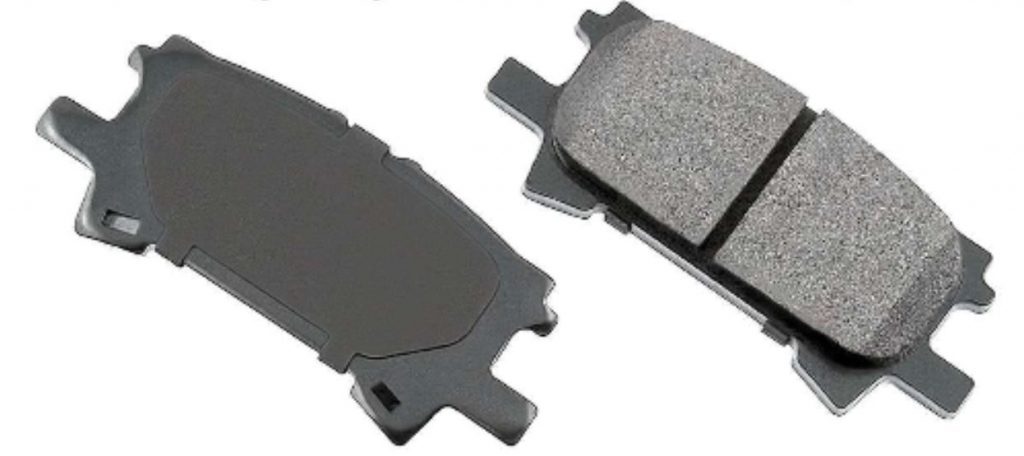
What if Genuine pads aren’t Available?
There are times when we don’t use genuine pads. When a car is relatively rare, we won’t stock the pads for it. Neither will the local dealerships. People have come to expect same-day service for the most part, and typically don’t want to wait for special order parts to arrive.
If we can’t get genuine, we’ll get the next best thing: OE, or Original Equipment.
Akebono is one such brand; they make the pads that come on many new Japanese cars. Replacement pads are manufactured in both Japan and in the USA, and they’re very high quality.
You may have noticed the “Akebono” stamped in the picture of the Subaru brakes above. You may also notice the Akebono printed on the friction material of the Toyota brakes on the left. Akebono makes pads for Honda as well.
OE brakes, while very good quality, aren’t necessarily the exact same thing as genuine. For one, a set of Subaru brake pads will come with new shims and hardware. Akebono pads don’t. The friction compounds may also be different depending on the application.
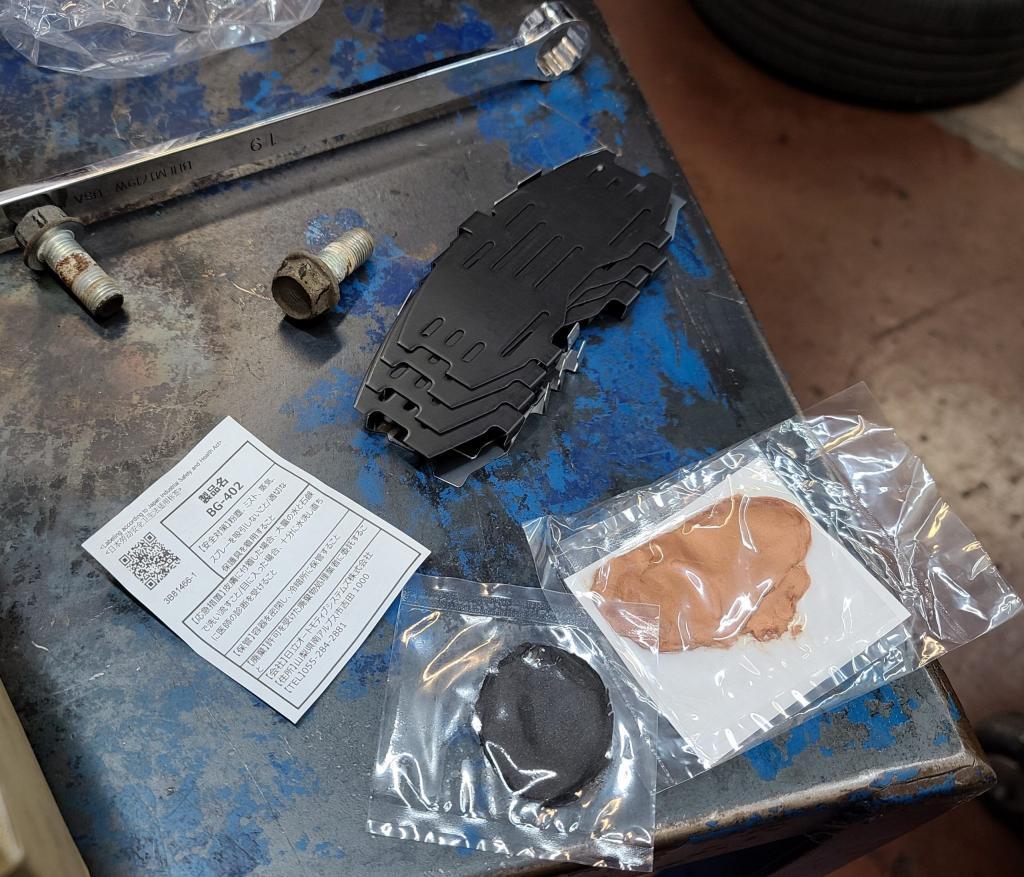
Molybdenum Paste
Doing brake work right is more than just buying good brake pads and bolting them in. One important aspect is using the right grease.
What’s the best grease to use for brakes? Well, it depends where it’s going. Different types of grease have different strengths.
Thick moly paste is only for the back of the brake pads and pad shims. This type of grease is too thick for lubrication. Its job is to dampen the vibrations that create brake squeal.
Most manufacturers will include a packet of this thick gray grease in the box with the brake pads.
If the pads don’t come with moly grease, then Honda sells tubes large enough for 100 brake jobs. Honda calls it M77 assembly paste. Of the moly pastes available, this is the one most like what comes in the packet with new pads.
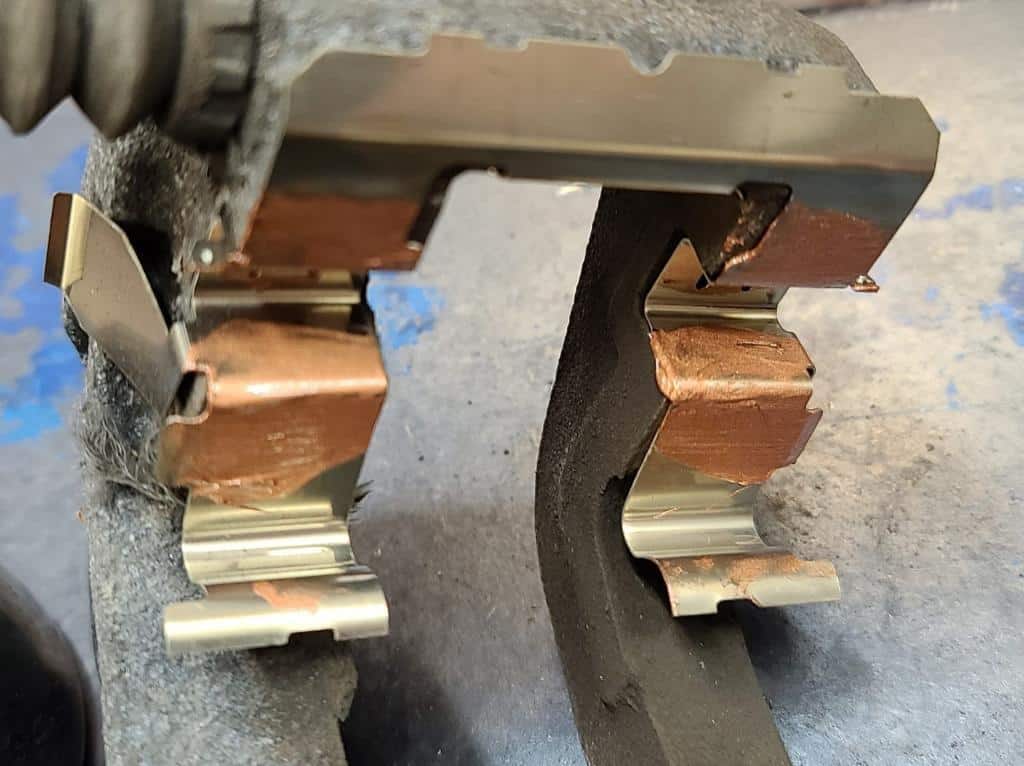
Copper grease
Copper grease is best for sliders and caliper brackets. Absolutely never ever use the packet of moly paste on the caliper sliders. This is a very common error.
It won’t cause the brakes not to work or anything, but it will cause the pads to bind in the calipers. You’d be much better off putting nothing at all on the sliders.
I like the copper grease that comes with Toyota and Subaru brake pads. Nissan used to make a bulk container of this grease, but they no longer do. It was an enormous jar so I’ll never run out.
I’ll probably end up passing the tub of grease on to my children. Ah the perks of being a mechanic’s daughter.
Caliper pin grease
Always clean and lubricate caliper pins. We once had a mechanic work for us for a short time. He did a brake job that didn’t work out so well. We found one of the caliper pins seized when it returned.
When we pulled him aside and asked what was going on he said that he didn’t lube the pins “unless they needed it”. So, in other words, unless the pins were already binding, he didn’t do anything to them. And since the pin was bound, he clearly didn’t even do that.
Sadly, this is a very common attitude in the auto repair industry. I frequently find cars with frozen pins and 3 newish brake pads, and one worn out pad.
Just like the other brake lubrication area, the pins require a particular type of grease. Silicone grease is best for the pins. It can handle high temperature. It won’t damage the rubber boots and pin anti-rattle bushings.
Once again, never-ever use the moly paste for anything other than the brake pads shims. Moly grease will cause the rubber to swell and the pins to bind.
Machining Brake Rotors
Brake replacement isn’t complete without addressing the brake rotors. A brake rotor is a metal disc that spins with the wheel. The rotor is the disc in the term “disc brakes”.
A brake caliper mounted to the knuckle squeezes the brake pads against the rotor which slows the car. Machining the brake rotor simply means cutting metal off the disc so that there’s a smooth, flat, and true surface for the pads to rub on.
The brake pads wear much faster than the rotors, but the rotors do wear. One reason to machine the brake rotors is to ensure good surface contact with the new brake pads.
The rotors and pads wear together over time and their shapes match one another perfectly. When the pads are replaced with new pads with a flat friction surface, they won’t match the convex shape of the rotors, and won’t have good contact. Less contact means less friction and less stopping power.
New pads will eventually wear to the shape of the worn rotors, but do you really want to drive around with less braking power in the meantime?
Another reason to machine rotors is to restore parallelism. If the brake disc is “lumpy”, you’ll feel it in the pedal and the car will shake when braking, especially on the freeway. Machining rotors restores the parallel surfaces for vibration-free braking.
TAKING TIME TO DO IT RIGHT
When the rotor is mounted to the lathe, it must be mounted so that runs true. If rust or debris is left on the hub face, the rotor will wobble on the lathe. If it’s cut flat while wobbling on the lathe, it will wobble on the car.
This is bad. There will be no noticeable problem at first, but after the car has been driven many miles, pad material will accumulate on the high spots and a brake pulsation will develop. What I’m saying is that unless you mechanic is knowledgeable and careful, he can introduce a problem that won’t show up for hundreds of miles.
Quality Repair?
The video on the left is a rotor that was cut by another repair shop. Several thousand miles later, they brought the car to us because it begun to shake violently when braking.
In the video you’ll see that the friction surface of the rotor has about 0.020″ runout. That’s about 10 times the maximum limit.
The rotor hub face has less than 0.002″ runout. When this rotor was machined, it was mounted crooked in the lathe, and runout was cut into the rotor. This would have been obvious to the lathe operator, which means he either didn’t know any better, or didn’t care.
As I said earlier, symptoms won’t develop for many miles after the brake job is complete.
Surface Finish
The other issue is surface finish. If a mechanic doesn’t spend the time to create a good surface finish, braking power will decrease, and noise will increase.
Surface finish is easy to understand. A good surface finish is smooth. A bad surface finish is rough. The smoother the brake rotor, the better the brakes will work.
Surface finish is affected by the following:
- The feed rate of the tool bits
- The rigidity of the lathe
- The sharpness of the tool bits
- The spindle speed
- The depth of cut
If a mechanic knows what he’s doing and is willing to take the time to do the job right, the surface finish can be made as good or better than the factory finish. On the other hand, if a mechanic doesn’t know how to improve surface finish or is more worried about how long the job takes than the quality, machining the rotors may worsen the braking rather than improve it.
conclusion
Our auto repair shop in Berkeley focuses on quality brake work, ensuring every brake replacement is done with with care and quality parts. Genuine pads from the dealer, proper lubrication, and a rotor with a smooth, flat surface that’s running true. That’s what makes a good brake job.
Proper brake service is pretty simple, but not all that common. Using cheaper aftermarket pads if far more common than using factory pads.
Sometimes a shop will use aftermarket pads so they can offer a more “competitive” price. Some shops charge genuine part prices for aftermarket parts so they can make more money. Sometimes clients are offered genuine pads but decline due to cost and insist on getting aftermarket pads.
Regardless, bad brake work, or at least what we consider bad brake work, is far more common than brake repair that is the same quality as what came with the car.
When you see shops advertise brake jobs for less than the wholesale cost of factory pads, you should know you’re not going to get the same thing; it’s not an apples-to-apples comparison.
If “Shop X” offers a front brake job for $49.95 and we quote $320, it’s not because we’re trying to rip you off. We’re charging fairly to cover our costs and make a reasonable profit.
Good mechanics command higher wages. Buying parts from dealerships means low margins. Paying workers hourly rather than by the job allows them to remain focused on one thing — quality.
Now you know how we feel about it, and you can make an informed decision. Happy motoring (and braking!)
Brake repair in Berkeley!
If you own a Toyota, Subaru, Honda, or Mazda, and are looking for brake replacement or service in Berkeley, CA, or nearby Oakland, Emeryville, El Cerrito, or Albany, give us a call. We won’t let you down. We’re serious about auto brakes and we care about quality.
Other resources
If you found this interesting, and you’d like some more technical information, you might also like the articles from StopTech. Here’s an article about bedding-in brakes. And another articles about what causes brake pedal pulsation. They do a great job of explaining the issues and engineering that go into making good quality brake components.
The Engineering Explained YouTube channel has some great content. In this video he goes to a brake manufacturer and reports on brake pad dynamometer testing to discover which kind of pads are best (spoiler: genuine).
In this video he talks about some new coating technology Porsche is using. Apparently, it works great, but a brake job is $32,260, without labor. Yikes! A brake job on a Honda is literally 1000 times less, not to mention the fact you could buy two brand new Honda Civics for the same price.
Here on our site, you may be interested in how to bed-in your brakes after a brake job, or why we still machine brake rotors while many shops won’t.